一、传统工业自动化是否仍能满足现代生产的“透明化”需求?
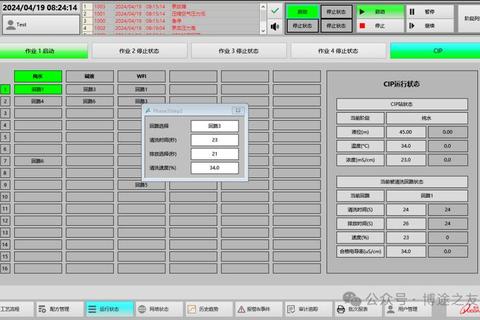
在工业4.0时代,某汽车制造厂曾因设备数据孤岛问题,导致生产线停机率高达12%。管理者发现,设备故障预警滞后、能耗数据分散在十多个独立系统中,这些问题让“精准掌控”成为空谈。高效智能WinCC组态软件全面赋能工业自动化精准掌控的价值开始凸显。
通过WinCC的SCADA系统,该企业整合了PLC、传感器和MES系统数据,实时监控覆盖冲压、焊接、喷涂等9条核心产线。系统上线后,设备故障预警时间从平均2小时缩短至15分钟,生产线综合效率提升23%。例如,在涂装车间,WinCC通过分析烘房温度曲线与能耗数据,优化了烘烤工艺参数,年节省天然气费用超180万元。这种数据驱动的透明化管理,彻底打破了传统自动化系统中“数据沉睡”的困局。
二、复杂工艺场景下,如何实现控制系统的“柔性适配”?
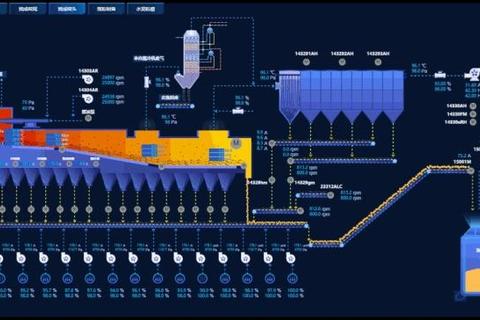
某化工企业曾面临特殊工况挑战:反应釜温度控制需在±0.5℃精度内波动,而传统PID控制方案在物料特性变化时频繁失准。引入高效智能WinCC组态软件后,工程师利用其内置的先进过程控制(APC)模块,结合OPC UA协议接入实验室分析系统数据,构建了动态参数调整模型。
具体实践中,WinCC的脚本引擎实时解析物料黏度、催化剂活性等12项关键参数,自动优化PID控制系数。项目实施后,产品合格率从89.6%提升至98.3%,年减少废料处理成本约350万元。更值得关注的是,该系统支持通过拖拽式界面快速重构控制逻辑,在应对新产品工艺变更时,组态效率提升达60%。这种柔性化控制能力,让复杂工艺的精准掌控不再依赖经验主义。
三、跨平台设备互联能否突破“信息茧房”?
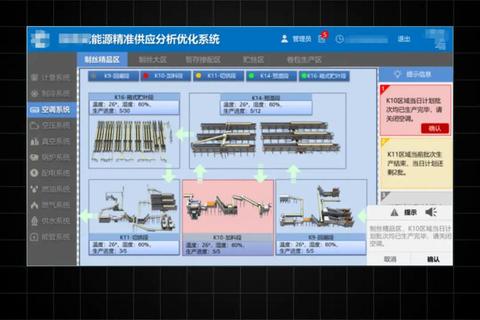
在某智慧水务项目中,市政部门需要整合27家供应商的200余套设备,涵盖施耐德PLC、ABB变频器、霍尼韦尔传感器等不同品牌设备。传统方案面临协议转换复杂、数据采集延迟高等难题。采用高效智能WinCC组态软件后,其支持的Modbus TCP、PROFINET、BACnet等18种工业协议库发挥了关键作用。
通过WinCC的统一数据平台,水泵机组、加药装置、管网监测设备的运行数据实现毫秒级同步。在雨季防洪调度中,系统结合气象数据预测模型,提前6小时启动排水泵站,使城区内涝发生率下降41%。该项目验证了WinCC在异构设备互联中的卓越兼容性——设备接入周期从平均3天缩短至4小时,跨系统数据交互效率提升17倍。
工业自动化转型的实战建议
1. 分阶段实施数据整合:从关键设备的数据采集起步,逐步扩展到全厂级监控,避免一次性改造的资金压力。某装备制造企业的经验显示,分三期投入可使投资回报率提升至226%。
2. 活用模块化组态功能:WinCC的图形库包含3000+工业标准符号,支持快速搭建个性化界面。建议建立企业级元件库,如某冶金企业通过标准化图元管理,使组态效率提升55%。
3. 重视安全纵深防御:在部署WinCC时,应采用V7.5版本的多层安全架构,包括用户权限分级、通信加密和操作审计日志。某核电站应用案例显示,该方案可拦截99.6%的异常访问尝试。
高效智能WinCC组态软件全面赋能工业自动化精准掌控的实践表明,工业数字化转型绝非简单的设备联网,而是需要构建“数据-控制-决策”的闭环体系。当某污水处理厂通过WinCC实现吨水处理能耗下降0.28kWh时,我们清晰看到:在智能制造的赛道上,选择对的工具平台,就是选择未来竞争力。
相关文章:
文章已关闭评论!